Root Cause Analysis (RCA)
Root cause analysis (RCA) is a methodology through which you can uncover the cause of a problem, allowing you to solve it at the root so the same problem won’t reoccur.
An RCA may therefore be used to uncover which corrective actions to take in order to re-stabilise or optimise a process, particularly within the context of being required to comply with regulatory rules like a HACCP hygiene code.
When critical control points (CCPs) have their limits exceeded and a hazard is detected, you or your investigators should go through a full RCA. This will allow you to get at the bottom of what caused the incident and then be able to adjust your processes where necessary, to ensure it won’t happen again.
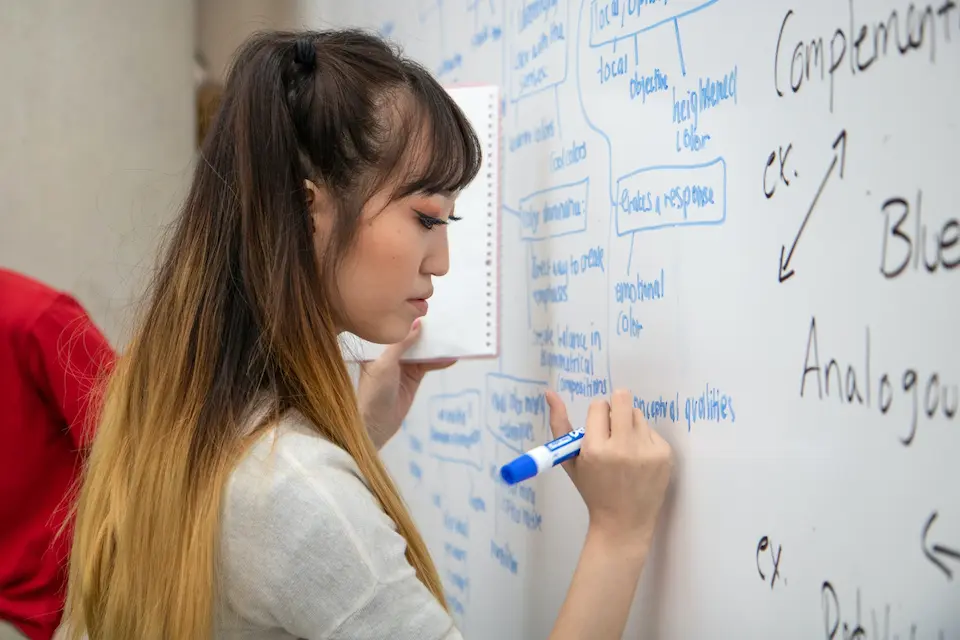
What steps make up a root cause analysis?
- Identify and clearly describe the observed problem.
- Determine the timeline of events between the normal situation and when the problem occurs.
- Spread out the different causal factors to get to the root cause
- Work out the causal link between the root cause and the observed problem.
Once a clear root cause has been uncovered, the fifth step would be to find the best solution which for preventing the issue from occurring again.