Implementing a Digital Quality Management System
Setting up and implementing a digital quality management system can be quite a challenge, if you don't know what to pay attention to. In this article, we’ll show you exactly what to look out for when implementing your digital QMS.
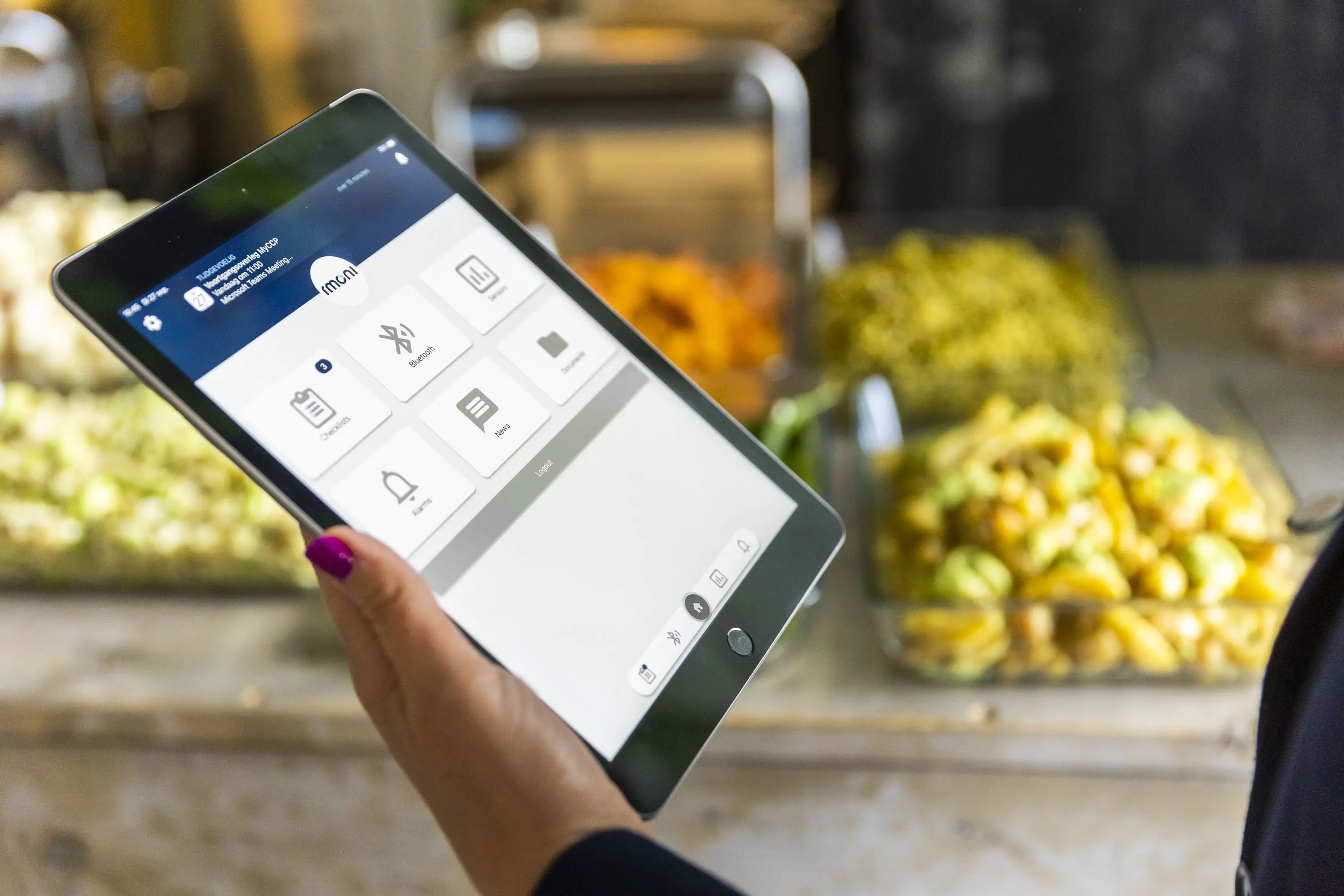
Digital quality management: what is it, exactly?
Digital quality management means you perform quality checks and manage your quality processes digitally, instead of using paper checklists and forms. Not only does this save you a lot of time, it also minimizes the risk of human error.
And where measurements of quality management parameters like temperature and humidity were previously done manually, with a digital quality management system, these are automated, too. Let’s take a quick look at the benefits of such a digitalized system.
Benefits of a digital quality management system
1. Fewer human errors
Let’s face it: human beings are often more prone to error than their digital counterparts. Computerized systems don’t get tired, sleepy, or hungry. When you digitize your quality management systems, you minimize the amount of errors made.
2. Automated reporting and dashboarding
Manual checklists, forms and temperature checks take time. And the results of all these checks need to be turned into reports, too. But when you use a digital quality management solution, all of your reporting and dashboarding is automated.
3. Always compliant with regulations
Implementing a digital QMS means digitizing all your quality management data, as well. And digitizing data means it’s all stored for future reference. Next time you face an audit procedure for compliance or regulatory demands, all this data is accessible.
4. No more drowning in paper chaos
Digitizing data also means you can say goodbye to the mess of manual checklists, forms and other paperwork. Decluttering your quality management processes means more focus where needed, and more efficiency in the long run.
5. Clear overview of the entire situation
With all your data neatly stored digitally, and automated reporting and dashboards rolling out because of that, you’ll have a bird’s eye view of your quality system and a level of oversight like never before. Pretty convenient, if you like your systems organized.
Implementing a digital quality management system in 5 steps
Step 1: Map out your current quality management system
First, you’ll need to get a good idea of your current quality management system, and clearly map it out. What are the processes already in place? Are these sufficient and compliant as is? Next, you might need to figure out which quality management system applies to your business.
Do you produce, process or distribute food or animal feed? Then you must first draw up a HACCP food safety plan. You can then choose to get certified, officially, according to different types of quality certifications. Think of systems such as ISO22000, BRC, GFSI, etc. You can also make use of an officially recognized hygiene code drawn up by your specific industry.
Step 2: Choose a digital quality management system that suits your needs
The digitization of quality management systems has taken flight in recent years and there are many parties in the market that offer solutions for various purposes. The trick is to choose the digital system that best meets the needs and wishes of your own organization. This is partly determined by the quality system you chose.
In any case, keep it as simple as possible. Complex quality systems will also lead to more (unnecessary) complexity in your organization.
Step 3: Install your measurement devices and hardware
Temperature is a CCP in all major quality organization systems and deserves extra attention. If you choose to permanently monitor the temperatures through a digital system, make sure installation is carried out before you start the digitization process. It’s important to choose hardware that fits your software solution, preferably fully integrated in a central platform.
The placement of sensors in your cooling equipment is extremely important, here. The measuring equipment’s purpose is to have the measured temperatures reflect the core temperature of stored raw materials as accurately as possible. The location in refrigerators/freezers is decisive here.
Step 4: Personalize your software
The software you’re using should be fully aligned with your original quality management system. This means all digital processes must exactly match the manual version of the system. You should be able to carry out all measurements and registrations in accordance with the original process and procedures.
It’s important that the software you end up choosing can be adapted to your specific organization's processes. And it’s also important that staff recognizes and acknowledges this. If they do, it makes adoption and implementation much easier.
Step 5: Set up processes to analyze your reports
By collecting data with your digital quality management system, you’re able to make simpler analyses and improvements to the process where possible.
Apart from this, recording non-conformities and noting the associated corrective action is very important. It leads to working in a way that guarantees food safety, demonstrably.
By including smart reporting in your quality management system, this flow of information changes from a once-off to a continuous data stream. This will, in turn, lead to a process of continuous improvement in your organization and food safety processes.
Things to look out for when implementing your digital QMS
When implementing a digital quality management system, there are a few key things to consider. It's important to understand the specific needs and goals of your organization, and design the system accordingly. This may involve conducting a thorough analysis of your current processes and identifying areas for improvement.
It's also important to ensure that the system is fully compliant with relevant regulations and industry standards, and to put in place adequate security measures to protect sensitive data.
Finally, it's crucial to provide ongoing training and support for your team to ensure that they are able to effectively use the system and derive value from it. This may involve providing access to resources such as user manuals and training materials, as well as offering technical support as needed.
Apart from these rather obvious ones, let’s take a closer look at some other things to look out for when implementing your digital QMS.
Correctly installing your measurement devices and hardware
The installation of your measurement devices and hardware will typically involve several steps, including the following:
- Identify the specific measurement devices and hardware that will be used as part of the system. This may include sensors, gauges, and other types of measurement equipment.
- Determine the locations where the measurement devices will be installed. This may involve working with other members of the team to identify the most appropriate locations for the equipment based on factors such as ease of access, accuracy of measurement, and potential interference from other equipment.
- Install the measurement devices according to the manufacturer's instructions. This may involve connecting the devices to a central control system, configuring the devices to communicate with each other, and setting up any necessary software or calibration tools.
- Test the measurement devices to ensure that they’re working properly and providing accurate readings. This may involve conducting a series of tests or calibrations to verify the accuracy of the equipment.
- Train any personnel who will be responsible for using the measurement devices as part of the quality management system. This may involve providing instruction on how to use the equipment, interpret the results, and troubleshoot any problems that may arise.
Overall, the key to a successful installation of a digital quality management system is thorough planning and careful execution. It is important to take the time to identify the right equipment and install it properly in order to ensure that the system is effective in providing accurate and reliable measurements of the product or process being monitored.
The placement of your measurement devices and temperature sensors
The placement of the temperature measuring devices in your refrigeration and freezing equipment is extremely important. The purpose of the measuring equipment is to have the measured temperature reflect the core temperature of the stored raw materials as accurately as possible. The place in the refrigerator/freezer is decisive here.
Things to look out for when it comes to temperature measurement devices and their placement:
- Installation should be easy, preferably without the intervention of a technical service department
- Make sure the sensors aren’t placed in any air streams
- Provide a simulation of the core temperature using a glycerol jar or sensors that include an algorithm to determine the core temperature
- Set up an alarm for when temperatures are exceeded
Guaranteeing a stable network connection
This one might seem obvious, but it’s very important nonetheless. If you’re going to install digital sensors, keep in mind the network connection should be as stable as possible. In practice, WIFI connections aren’t always as stable as can be.
It’s better to create your own network for the sensors, such as a Zigbee network. Additionally, use measuring equipment with its own memory to ensure that, in the event of unexpected malfunctioning, measurements are still recorded and saved for future reference.
Personalizing digital check- and measurement lists the right way
When you map out and set up registration lists, make sure they match your organization’s processes in a recognizable way. This means both in terms of registration points as well as in terms of frequency of registration. If this is fully in line with your actual processes, the set up won’t raise any questions among employees.
By setting up the system correctly, you’re not only complying with mandatory registration requirements, but the system also becomes easier to use during employee instruction.
Clear training and instructions for staff operating the digital QMS
When implementing the system, it’s important each and every one of the employees who’ll be working with the system are trained in using it. Make sure they know answer to questions such as:
- How does the system work, exactly?
- What I’m expected to do, i.e. what’s my role?
In addition, this is also an excellent opportunity to refresh your employees’ memories when it comes to the food safety system used in your organization. Use this moment to remind everyone of their responsibilities and how the digital system will help them fulfill those.
Additional instructions for when things go wrong
If a non-conformity is found during the filling out of registration lists, it’s mandatory to include a corrective action. This action must lead to the prevention of a potentially food-unsafe situation by reacting appropriately. That entire process should be documented, too, leading to lots of potential manual administrative work.
By digitizing the system, it becomes possible to predefine the corrective action and help employees to take the right action each and every time..
Setting up remote access to the system
The digital quality management system’s accessibility should be as user-friendly as possible. We recommend choosing an app-based system, where access can be granted to specific users. Apart from easy access, make sure you set up custom access rights. This means anyone who uses the system only has access to the digital system’s data and associated tasks relevant to them.
It’s also crucial to make someone in the organization responsible for the digital system in its entirety, so it’s always up to date and the right users get – and maintain – the right access levels.
Choosing the right type of automated reporting
The system’s reporting setup must be drawn up as specifically as possible. While you’re doing this, make an effort to minimize reporting, too. Printing reports creates a lot of paper we’d rather be rid of. It’s best to make registration transparent via dashboards or widgets.
Only print reports if absolutely necessary or at the request of, for example, inspection authorities. Even then, it’s preferable to only print digitally in PDF format, for example. Alarms must also be set up digitally.
Making sure you minimize paperwork as much as possible
By digitizing as much as possible and using digital reporting only, you’re left with a minimal amount of paperwork. If your digital quality management system also offers the option of uploading or photographing documents, it’s possible to set up a completely paperless system.
All documents are then centrally located in a system, always accessible. Say goodbye to an organization filled with file cabinets and paper checklists.